安川焊接机器人搭载WGFACS节气系统,是实现保护气节约的核心。该系统凭借高精度传感器,实时捕捉焊接过程中的电流、电压、熔池温度等关键参数。基于复杂算法模型,系统能精准识别焊接起弧、焊接进行、收弧等不同阶段的特征。起弧瞬间,自动降低保护气输出量,避免起始阶段气体无谓消耗;焊接过程中,依据熔池动态变化和焊接速度,实时调整气体流量,在确保熔池充分保护的前提下,减少多余气体排放;收弧时,及时减少气体供应,杜绝气体浪费,实现全流程精准节气控制。
针对不同焊接材料对保护气的特殊需求,安川焊接机器人具备强大的自适应调节能力。焊接碳钢时,系统自动优化氩气与二氧化碳的混合比例,在保障焊缝强度与成型质量的同时,降低气体使用量;面对铝合金等有色金属焊接,精准控制高纯氩气流量,在满足焊接工艺对气体纯度和保护效果高要求的基础上,提升气体利用率。这种基于材料特性的智能适配,避免因气体配比不当造成的浪费,进一步强化安川焊接机器人节气效果。
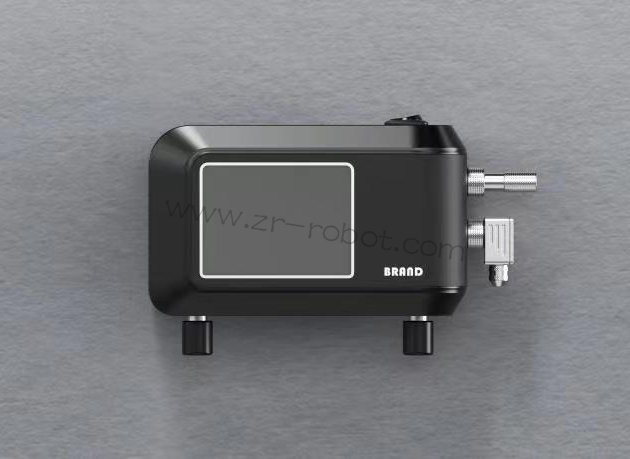
安川焊接机器人的控制系统与保护气供应系统深度融合,达成多维度协同节气。在焊接路径规划环节,系统结合路径信息预测气体需求,提前调整供气参数,减少无效路径的气体输出;在参数调节方面,根据焊接任务自动匹配电流、电压等参数与气体流量,避免因参数不匹配导致的额外气体消耗。此外,系统还具备气体管路状态监测功能,一旦检测到泄漏或异常,立即发出警报并采取措施,防止气体损失,全方位提升安川焊接机器人节气效率。
除了上述功能,安川焊接机器人还能通过数据积累与分析,不断优化保护气节约策略。系统持续记录不同焊接任务下的气体消耗数据和工艺参数,通过对大量数据的挖掘分析,总结出各类工况下的最佳气体使用模式和参数设置。随着作业数据的增加,系统自我学习能力不断增强,节气策略愈发精准高效,为企业带来持续的成本节约效益。
实际应用中,配备WGFACS节气装置的安川焊接机器人展现出显著成效。在大规模焊接生产场景下,保护气体消耗量可降低30%-50%,特殊场景降低达60%,大幅削减企业气体采购成本。同时,精准的气体控制有效提升焊缝质量,减少气孔、夹渣等缺陷,降低因焊接质量问题导致的返工率,间接节约人力、时间和材料成本。
WGFACS节气装置通过智能监测、自适应调节、系统协同和数据优化等多方面技术创新,实现了保护气的智能节约。这些技术不仅为企业带来直接经济效益,更推动焊接生产向绿色、高效方向发展,充分彰显安川焊接机器人节气的应用价值和发展潜力。